

With the slider into the main base and using a drill bit ø4mm (upside down) adjust / center the pieces (main base / slider / waste of cutting) and keep in place by a clamp. Clean up the edges of the piece and do a ø4mm hole at the center. Now it's time to use the waste of cutting that we have kept from a previous step. Now we must cut and remove the extra length from slider.įor this cut I have use my disk saw machine but you can use your angle grinder with cutting disk 1mm as well.ĭrill a hole ø4mm and depth 10~12mm at the center of slider's upper edge side.įrom a flat bar 30x3mm cut a piece 18mm and do a ø4mm hole at the center. Reassembly bushing bases / bearings / shoulder bolt / bronze spacers / roller. The solution is too simple and quick but a disassembly of bushing bases.is needing.Ī small cut with a hack-saw at the bushing's base upper edge and some smoothing by a file and it's ok. When the slider is at the lowered point then the upper roller must be in touch with lower roller.īut the bolt’s nut of upper roller is touching over the top of the bushing base at the back side leaving a small gap between the rollers.
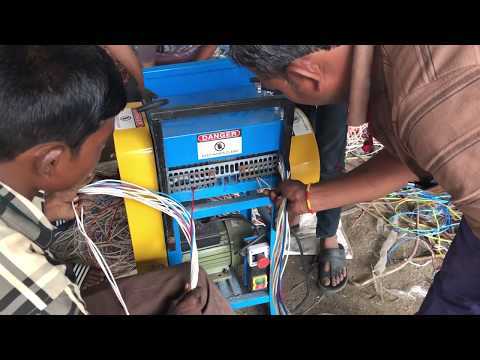
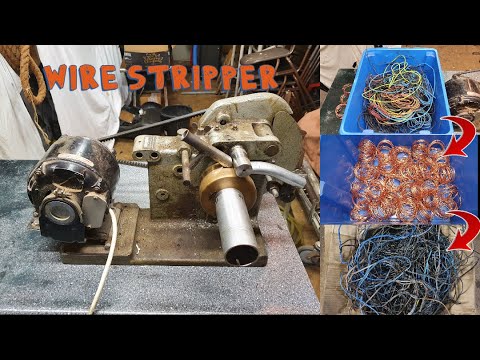
If you decide to use a M12 Shoulder bolt, then just increase the diamete of the hole to 12mm.Īlso need to increase the diameter of hole from 10mm to 12mm at the front and middle piece. If you decide to use a regular M12 Allen socket head bolt then you will need to cut a M12 thread at the back piece. Then do a countersunk about 3.3mm depth and dia12mm so to fit a countersunk head bolt M6. The middle piece must be now at 5mm distance from the edge of outer pieces.ĭo a center punch mark at 20mm from the left/right edge and 45mm from bottom edge at the front piece.ĭrill a ø5mm hole at the three pieces simultaneously.ĭisassembly and then at the back piece cut a M6 thread.Īt the front and middle piece increase the dia of the hole to 6mm. Using a M10 bolt/nut mount/align/center the three pieces and tighten the bolt/nut. Temporarily we will make the diameter of the holes where will be rest the shaft of roller ø10mm.Īt the piece of 75x30x8mm do a center punch mark at 15mm from the left/right edge and 10mm from bottom edge.įrom the 40x5mm flat bar cut 2 pieces 75mm each one.Īccording the plan we need 2 pieces 65mm but this extra length will help us later to do at once a straight and symmetrical cut, at the three pieces that slider consists.ĭo a center punch mark at 20mm from the left/right edge and 15mm from bottom edge at the first piece.Īlign and secure both of them at the vise and drill the hole at both simultaneously.Īfter you has finish the boring of the holes at ø10mm use a countersink or a ø16mm drill bit and clean up the edges of holes. Using a countersink clean up the edges of the holes.Īssemble main base - bearings - bushing bases. Increase the center holes to ø10mm and then to ø16.5mm. Increase the holes that will pass the four M6x45mm bolts to ø6mm. We will use it later.įrom a flat bar 8mm thick cut a piece 75x30mm and refine / smooth the edges by a file also do an orientation marck. Using an angle grinder with 1mm cutting disc, make the two cuts.ĭon't throw out the piece of wastage. Make a jig so to hold it the pieces in correct place aligned and do center punch marks using a Center Punch ø3mm at the points that must become the 5 holes. Using a vise you can drill them simultaneously. Using aniline paint the marks will be very clear and easy to view.Ī number punch mark at the pieces is useful as you will be able to use the same orientation at the whole of building process till to the final assembly avoiding the errors.ĭill the 5 holes at the two pieces of 40x40x5mm. Prepare/cut a piece of flat bar 120x8mm at 115mm and two of flat bar 40x5mm at 40mm.Ĭlean up the surfaces of pieces so to become smooth enough. For the roller rotation I have use the motor from an old battery hand drill (14vdc) and one of my two bench top regulated power supplies 10~18VDC/30A & 2~24VDC/10A (both can drive the motor and do the job).ø30/12x20 mm smooth roller DIN CK60 1pcs.
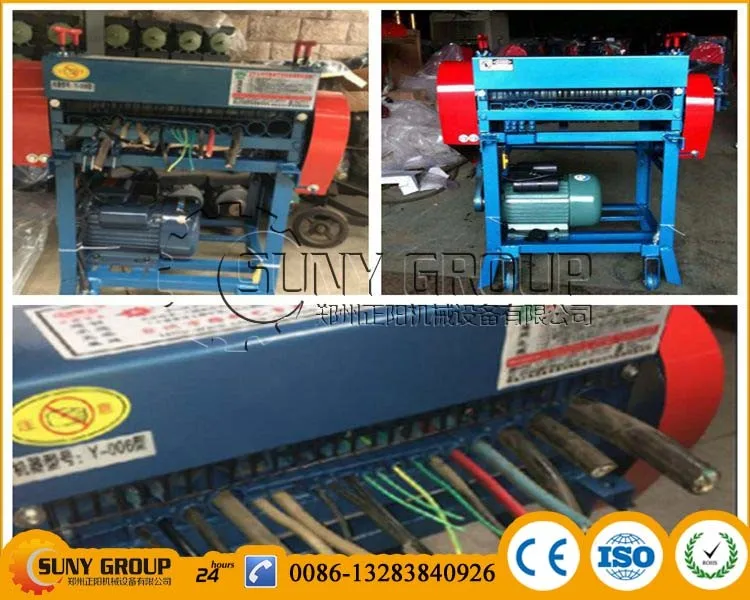
